In this post, I am laying out a broad overview of the factors I have learned to consider when attempting to achieve a certain color. None of these factors is considered in great detail. The next post will contain a list of resources which can help you flesh out the information here..
Before dyeing yarn, I had tie-dyed once before. When I was in high school, I volunteered at the Boston Children’s Museum. One of the times I was there, they asked me to run a demo and help kids tie-dye small bits of fabric. That was a long time ago! I did have other relevant color experience, though: cake decorating. Most of the techniques of cake decorating are not relevant to knitting, but the way color works in cakes is relevant to the way dye works with yarn. If you look at most general color theory books, they are based on the way paint works. Paint color is not the same as dyeing or cake decorating, however. Paint colors are mixed with each other and applied to a surface, with the expectation being that they will mostly sit on top of that surface. Yarn and frosting both start out as white. The dyes are added into these white bases. The base itself has a profound effect on the color you get.
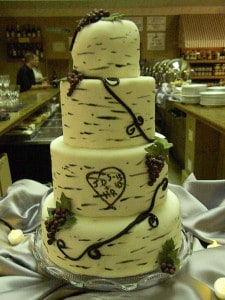
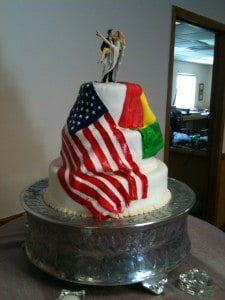
While the basic way dyes work is similar in cake decorating and yarn, dyeing yarn is a more varied and complex process. With cakes you have 3 or 4 basic types of frosting and while there is some variation in the way color works between them, the variation is considerably less than in yarn. When decorating cakes, I always made enough of the color to do the size job I needed to do. There was never an attempt to replicate an exact shade. When dyeing yarn, you can take that approach, but you can also choose to take an approach where you could potentially repeat a particular colorway. Doing so involves much more detailed attention to the way you create a color in the first place.
Dyes
You have 3 choices of dyes: acid dyes, fiber-reactive dyes, and union dyes. Acid dyes will work on protein fibers like wool and silk as well as certain synthetic fibers like nylon. Many people start dyeing using food safe dyes like Easter egg dye tablets, Wilton food colors, or Kool Aid packets. These are all forms of acid dyes. Professional acid dyes are not food safe, but tend to be more colorfast than the food safe options. Fiber-reactive dyes are used for cotton, bamboo, and other plant-based fibers. Union dyes (RIT dye, for example), are designed to work on whatever kind of fiber you have. One problem with union dyes is that you will usually end up with a lot of unused dye in the dye bath after your fiber is dyed. This happens because union dyes are basically a blend of several types of dye, ensuring that one or another part of the formula will work on your fiber. Your fiber absorbs the portion of the dye that it needs, leaving behind the portion that is unusable to that fiber.
Yarn
The properties of yarn affect the way it takes dye. This includes the fiber blend, chemical treatments like those used to create superwash wool, the number of plies, and the tightness of the twist in each ply. Many people, including me, start out using superwash wools so you do not accidentally felt the yarn while you are learning. Superwash wools tend to take colors more brightly when compared to non-superwash wools. If you are using acid dyes, and your fiber includes plant-based fibers, those fibers will not absorb the acid dyes and you get white heathering in your yarn. If your yarn is tightly twisted, it is more difficult for the yarn to absorb the dye. If a multi-ply yarn contains plies of different fibers or twist, the individual plies will absorb the dye differently.
Acidity
Most dye tutorials recommend using either citric acid of vinegar as a source of acid. Most dye instructions specify a certain amount of acid per weight of yarn to be dyed. However, by changing the acid level, you can get different effects in the color of your finished yarn. Messing with the acidity is one way to “break” dyes so that rather than getting a solid color, you get patches of the constituent colors (oversimplifying a bit as an example: blue + yellow = green; breaking a green dye means you see the blue and yellow rather than the green). You may also get more muted colors by adding less acid to the dye pot. A picture of this effect can be seen in a photo on page 14 of Hand Dyeing Yarn and Fleece, depicting two skeins of yarn dyed with the same dye stock, but different acid levels.
Water
None of the dyeing resources I have seen talk about water. This is an oversight, in my opinion. Water is the basis of all dyeing, from soaking the yarn to mixing the dye stocks to applying the dye to the yarn. Water varies from country to country and from one region to another within countries. In the United States, most municipal water is adjusted to a neutral 7.0 pH. Here in Florida, however, my municipal water comes out of my tap at somewhere between 8.0 and 9.0. Chris and I have been growing hydroponically for three or four years, so I was already aware of this situation before I started dyeing.
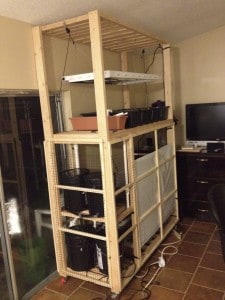
If I was not aware of the alkalinity of my water, and I was blindly following most dyeing tutorials, I would have found them frustrating. Adding a tablespoon of citric acid per pound of yarn, or whatever the recommendation is, would not necessarily get me brightly colored yarn because it may be insufficient to overcome the natural alkalinity of my tap water. For this reason, I adjust the acidity of my water using the pH meter.
A major reason for the high pH of our tap water is that it is groundwater with a high natural mineral content. Due to the hydroponic growing, we measure the total dissolved solids (TDS) of our water. The TDS of our tap water is high, around 200. I do not know exactly what the minerals in my tap water are; I would have to send samples to a lab for analysis if I wanted to know. However, there’s a good possibility that the minerals in my water react with the dye and change the colors I am able to get on the yarn.
At some point, I plan to run experiments using the same dye stocks in various water sources — tap water, bottled drinking, bottled distilled water, and rain water (we have a rain barrel) — so I can understand the extent to which water affects the final color of the yarn.
Dye Application Method
Dye can be applied to yarn in three primary ways: immersion, hand-painting, or dry. I believe that every form of dye application I have seen is a variant of these three basic methods.
In immersion dyeing, the yarn is immersed in a relatively large quantity of water. Dye can be added to the pot either before or after the yarn is added to the pot. Different colors of dye can be added sequentially to create layered effects. Variegated yarns can be created through immersion dyeing by tightly twisting the yarn so that certain areas do not soak up dye (called ‘resisting’) then untwisting or twisting in a different direction or angle and immersing in a different color dye.
In hand-painting, the dye stock solution is applied directly to the yarn. The yarn may be dry or wet before the dye stock solution is applied. The dye stock solution can be applied with a paintbrush, by squeezing it out of a bottle and then working it in by hand, or by any other method you can think up. The important feature here is that the dye stock is applied directly to the yarn.
Professional acid dyes come in powdered form. You usually mix them into a dye stock solution, but you can also apply small quantities of dry dye directly to the yarn. You do need some sort of water in the process. If the yarn is wet when you apply the dye, you will most likely get spots of color in the areas where the dry dye is applied. You can also put the yarn in a shallow pan, sprinkle dry dye over the yarn, then add water to cover. With this method, you end up with blocks of color. Breathing in powdered dyes can be a health hazard and you may develop allergies to dyes through repeated exposure. Whenever you work with dry dyes, you should wear a mask sufficient to filter out the dyes you are using.
Heat Application
Acid dyes require heat to set. You do not want to heat silk yarns above 185 degrees Fahrenheit because it destroys the luster of the yarn. Regardless of fiber content, yarn is generally not heated higher than the boiling point of water.
Immersion dyeing happens inside a vessel of some sort. Usually this means a pot on a stove. Immersion dyeing can also be done inside a crock pot. Another option is to put yarn and dye stock into a canning jar filled with acidic water. Sealed canning jars can be left out to heat in the sun (solar dyeing), placed into a roasting pan filled with water and then into an oven, or placed on a cookie sheet and placed into an oven. Yarn can be dyed to a semi-solid in this fashion, but canning jars are more frequently used for gradient or self-striping yarns. The skein is split into sections and each section is placed into a canning jar with a different color dye.
Hand-painted yarns are usually steamed to set the color. After color is applied to the yarn, it is wrapped in saran wrap. Steaming can happen in a microwave, in an oven, or in a pot on the stove. Some amount of water is added to a vessel, the saran wrapped yarn is placed inside that vessel, and the whole thing is heated until the yarn is hot enough for the color to set.